As we saw in an earlier post, flax is a very versatile plant which will grow just as happily in a back garden as in the depths of the countryside. So as you ponder, plan or plant your own sea of blue, please enjoy and be inspired by our little gallery below.
Take off your Crowns!
By Hermann Glaser-Baur
I felt honoured though and think that the “bigger picture” the just released piece fits into (or doesn’t fit into) requires a closer look and those who “add it to their playlist” (or not) need to be asked what their criteria for censorship (I have no better word) are.
And I think, Joe and his amazing song-writing should be placed amongst the numerous artists in all countries who look for the truth, who ask for justice, equality and – in his own words – “the treating of ordinary people with the respect they deserve”. We’ll attempt that at the end of this reflexion.
“Keep the fight in your hearts” is typical for his unique style of song-writing, he is able to put more meaningful words into a title than many others use nowadays to make up a whole song.
His lyrics make sense, they can be understood by ordinary people – like those whose houses are crumbling in Donegal or like those who “have no home to go to” in his songs about the shame of homelessness in the 21st century.
The very big and extremely positive response “Keep the fight in your hearts” is getting – recognition by the main-stream-media or not – proves this understanding and it shows the burning hunger for truth and justice many people, especially young ones, feel.
I would guarantee that the appeal to politicians in the song “… Take off your crowns and stand with the people…” will cause spontaneous applause in any concert.
Joe’s excitedly awaited appearance at the Flax Mill Yard Fest in September will show!
Just by the way: If it is this (rather modest, I would call it) appeal that makes the “powers to be” not have the song on their play – and other –lists and agendas – what can we learn from that?
Nothing has changed, tolerance, will for real change, even basic humanity and ruling politicians have been and are contradictions in terms.
Joe is not alone, historically and in the now:
Rambling Jack Elliot, Woodie Guthry, and Pete Seeger were disliked by the authorities (to put it mildly) in their home country USA. Billy Braggs and Dick Gaughan share their fate in the UK and Scotland, Hannes Wader’s songs weren’t played on German Radio for many years, Victor Jara was murdered in his home – land Chile because of his stubborn singing against the military regime.
These are but a few examples of artists who sung, spoke, and sometimes shouted the truth. They have one thing in common: The ordinary people like them, the authorities don’t. What does this say about the authorities?
These people, Joe included, are extremely important, especially today when too many have gone silent (or given in to being silenced).
The event is “invitation only” – if you want to be there, contact us now, also for a full programme:
“Dirt to Skirt” – the How-To Guide to Flax
The NeedleSketches Eco-Friendly Bread Bag
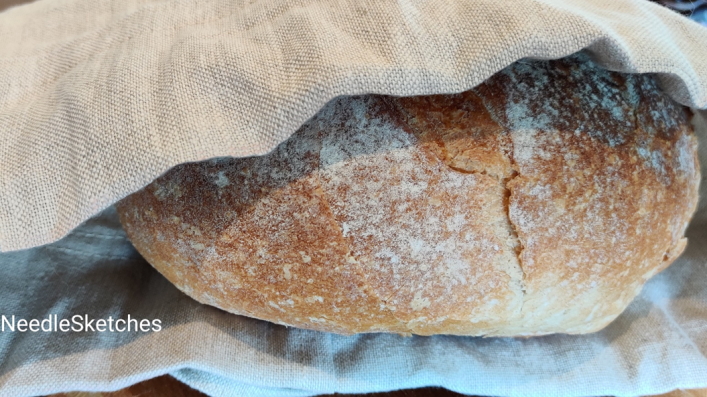
We are pleased to introduce a guest post from fellow crafters at Needlesketches who have found an innovative use for our ever-versatile Linen! Their Eco-Friendly Bread Bag made using Irish Linen is perfect to store freshly baked market or homemade breads.
When creating a bread bag, you require a high-quality fabric to make a high-quality product. For a bread bag, linen is the perfect fabric for the job. Linen’s antibacterial properties enable the fabric to behave as an ideal storage bag for freshly baked breads.
Linen can withstand reasonably high temperatures when washed and is a hygienic product which can be re-used. Linen is an Eco-Friendly fabric, hard wearing, can be laundered numerous times and can last for years.
This Eco-Friendly Linen Bread Bag has closed seams on the insides of the bag. It was design with hygiene in mind and to prevent crumbs catching in the seams.
The bag is designed such that the linen folds in on itself when the bag is closed using the double draw string closure; this closes the bag neatly and gives a seal that ensures that the bread is enclosed in linen.
Linen is the perfect fabric for bread bag!
“Weaving is a process used to create fabric by interlacing threads”
Here at NeedleSketches we consider this bag to be both eco-friendly and economical.
I like the idea of weaving threads together to produce a quality product which by its very nature is good for the earth. A chat with a wonderful food producer led me to thinking about the value of a simple linen bread bag – small changes can lead to amazing results.
Linen is biodegradable, whilst it is hard wearing it will also degrade and will naturally fall back into the earth. Replacing the storage of bread in plastic bags by using these linen bags works well for the environment and for your pocket. Linen helps to keep bread fresh for longer- saving money and reducing waste.
I also wanted to use natural locally produced products. There are a small number of Mills here in Ireland and I was delighted to speak with two amazing Irish Linen Weavers – Hermann and Marion of Flax Mill Textiles. They gave me a marvellous choice of linen, all woven here in Ireland.
With such a beautiful material, I set about designing the Eco-Friendly Linen Bread Bag, perfecting seams, closure, and size. Another wonderful chat with Michele of MarketStreet.ie led to the opportunity of selling online with MarketStreet.ie in March.
Following pleasant conversations with businesses from the Flax Mills in Dungiven to MarketStreet.ie in Dublin, this simple Eco-Friendly Bread Bag was designed and handmade in East Cork by NeedleSketches.
The Eco-Friendly Bread Bag is now available to purchase online at NeedleSketches Store on MarketStreet.ie – small changes weaving a positive impact on our world.
About Needlesketches
NeedleSketches design and make fabric bags, purses and more. Our attention to detail, coupled with the beautiful linen, cotton, cork oak and tweed fabrics used to make these handmade products ensure that you are always impressed by the quality of the items you receive.
Please visit the online shop or contact us through social media:
Past, Present and Future of Linen in NI – Three part mini series
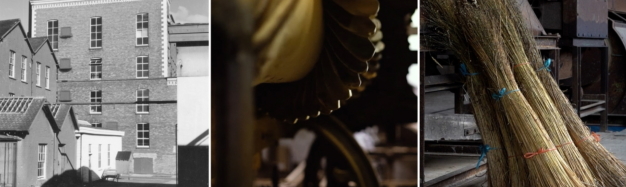
The Northern Ireland Science Festival 2021 has put together an eye-catching little series of vignettes detailing Irish Linen through the ages. Anyone who has visited our Open Days or frequented The Flax Mill on a regular basis should see some familiar faces in the films, friends who share our passion and vision for Irish Linen into the future.
A new addition to Dearbhla’s band!

Dearbhla McTaggart is well known here at The Flax Mill for her enchanting performances on the Irish Harp at the Yard-fest concerts while her playing is a perfect accompaniment to grace our fashion shows. She is also widely known in the folk scene, having played to thousands as far afield as Germany. We are very happy to announce she has added a new member to her merry band, her baby boy Donnacha! We wish them both health and happiness and look forward to watching him following in the footsteps of his talented Mother!
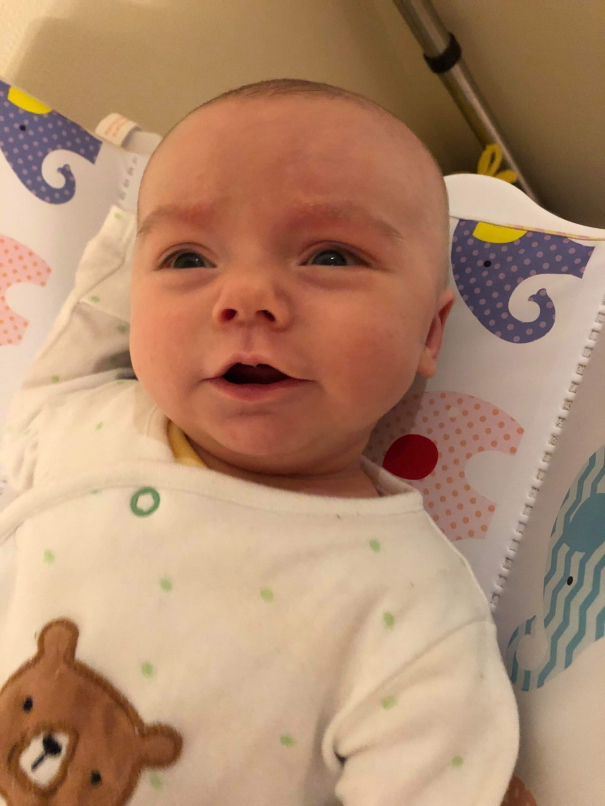
Flax spinning back to the future
Allow me to share a little yarn with you about how I came to be the proud owner of this delightful linen runner with more than a little help from Flax Mill’s owners, Hermann and Marion Baur.
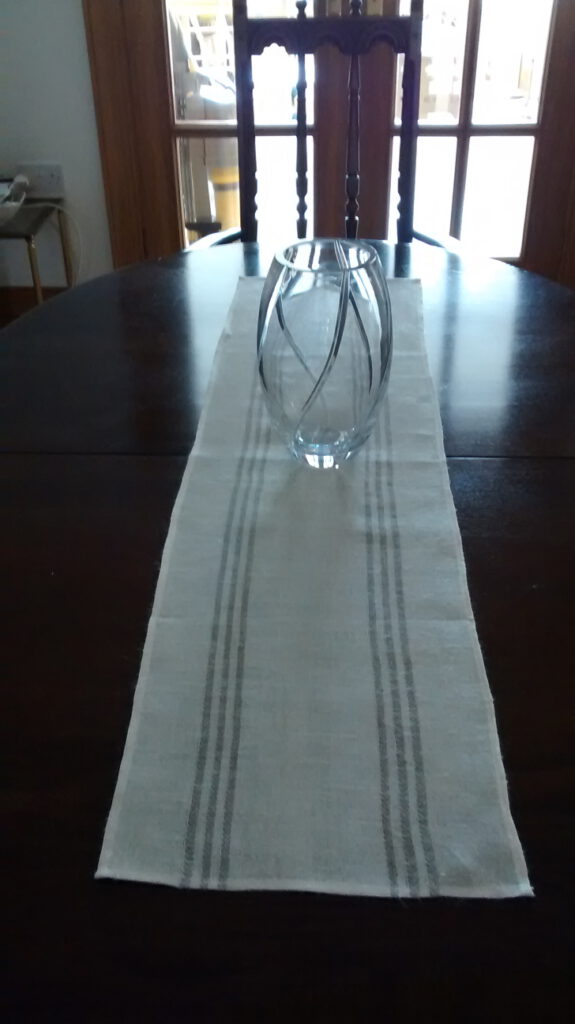
A little of my own background is first necessary to act as the warp upon which this little tale is woven. My name is Tiernan Stuart, though I also answer to Webmaster and Web Bastler (Bastler is German for tinkerer) here at the Flax Mill. My main duty is to ensure the website is always up and running, a job helped by a sojourn as a software engineer and a passion for flax and linen, first awakened back in the mid-nineties as a fresh-faced research student, eager to elicit new understanding from the secretive and elusive flax fibre. My first mentor Fred Sloan, pioneer of the Linron process for manufacturing linen blends, set me the task of discovering the formula for crease-proofing linen, possibly one of the oldest problems in the world still yet to be solved. I then joined a multidisciplinary team to tackle the thorny issue of improving the excellent Mackies’ Linmack 5 spinning machine, a task sadly cut short by the demise of the company itself.
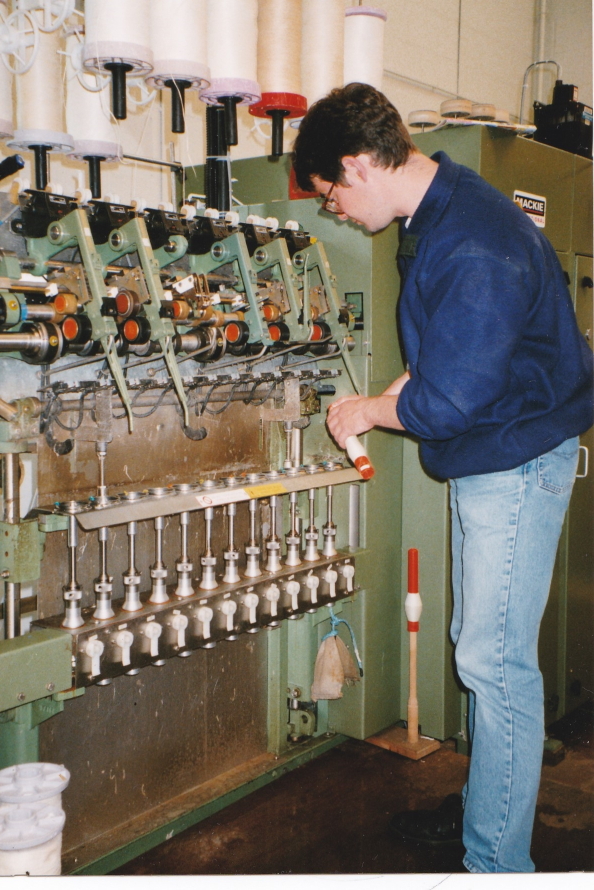
After a stint in Germany, funded by the German Academic Exchange Service (DAAD) to work with Professor Kessler on flax and hemp quality analysis, I was lucky to land a research post with Professor Sharma at Queens University Belfast, the author of the famous ‘Big Green Book’, “The Biology and Processing of Flax”: a copy of this very informative work is accessible through The Flax Mill library on request. Research there ranged from the the practical, studying flax-reinforced composites, through to the theoretical, examining the mechanism by which flax fibre so efficiently moves moisture along its length. Sadly funding ran out for the work and I was forced to retrain in computer programming in order to earn my keep.
Thankfully, after discovering the Flax Mill, my newfound software skills were put to good use promoting the cause of Irish Linen. Marion’s prodigious talents with the weaving frame inspired me to abandon my industrially influenced roots and adopt the artisan’s approach. I invested in a Louët S10C spinning wheel with the aim of tackling a vital missing link in Irish Linen production today, the making of yarn.
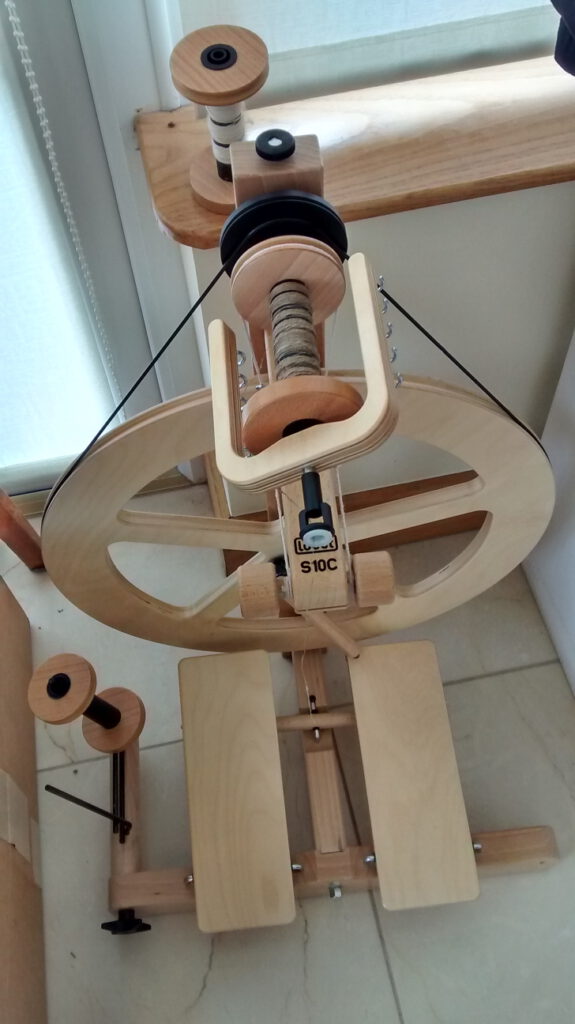
My early attempts were fraught with error though eventually, with helpful guidance from expert spinner Lorna Shannon, proprietor of Crann+Caora, I managed to spin something that vaguely resembled the yarns I had once produced on the Linmack pony frame. On my next visit to The Mill, I brought my yarn along for Hermann and Marion to cast their expert eye over. Marion whisked my improvised bobbin off the table with a gleam in her eye and a promise that a use could be found for my homespun efforts. On my return a few weeks later, she presented me with the runner shown above, a truly elegant setting to exhibit my humble efforts. For warp and weft, she used a combination of now rare Irish machine-spun yarns, detailed in the caption of the image below, whose manufacturers have long since passed into the history books.
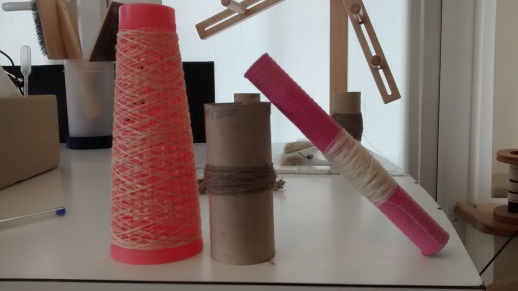
Marion’s skill managed to work wonders with my yarn as can be seen in a close-up of the runner’s decoration below.
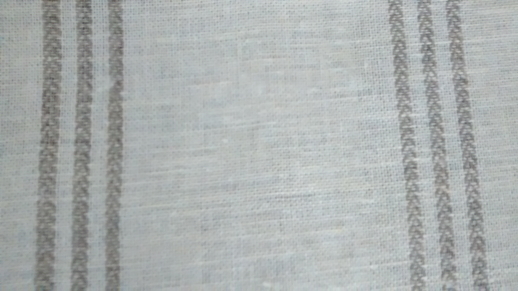
The runner now occupies pride of place on the dining room table as a reminder that the days of Irish Linen are far from over.
A Journey in Linen
In these days when many people feel restricted in their travels, some are even told to stay at home (that’s if they have one, I suppose), I found it fascinating to observe and put to paper the journeys of a machine.
A few years ago – we still operated our textile stall at the Belfast market then – a man from Ballymena approached me there. He told me the story of his father’s weaving loom. The fly – shuttle hand operated loom was used to produce “piece work” for “the big place”.
Like many linen towns, Ballymena had a large weaving mill, “Phoenix Weaving”. The partly water-powered and highly mechanised factory ran well over 300 power – looms and manufactured large quantities of Irish Linen. One of the earlier ones to close down, Phoenix is almost forgotten about nowadays. If anyone ever feels like reading through some of their wages – books, production day – books, cloth sales records etc., we have quite a few of them here in our textile – library.
The mill kept hand – loom – weavers in work, most of them working at their own homes. Despite the speed of the power – looms, the hand operated machines had (and have) their special qualities: High quality, short runs and bespoke fabric are easier done on them plus the operators are usually well trained and skilful. This kind of “home-work” still exists in the tweed-weaving of Donegal today.
Back to the Ballymena – loom, the man was looking for a home for it, we didn’t like the thought of it going to waste and told him, we’d come to see it soon.
No need to do this – the loom landed at Flax Mill a few weeks later. Dismantled into every bit, the gables were stripped onto the roof of an estate car, all the other parts inside – the first leg of the loom’s journey ended in Derrylane.
It turned out to be quite a sophisticated piece of kit:
48-inch weaving width (very wide for the time it was made), a top – hung fly – shuttle device with extraordinarily large shuttle boxes, it would have been pretty much “top of the range” when it was made by Youngs of Gallowshields I Scotland. It seemed complete, wooden parts and especially the gables strong and we put it into storage.
Several weavers and other textile crafters had a good look at it but nobody seemed confident enough to “go for it”.
We were contemplating restoration ourselves and putting it into the mill. At the same time, befriended master – spinner and weaver Lorna Shannon – many readers of this story know her as secretary of the Ulster Guild of Spinners, Weavers and Dyers – joined the maker’s house at the Designery in Bushmills.
She moved her own – much smaller – loom to the outlet which unfortunately had to close for a while due to the horrible circumstances caused by the virus epidemic. Lorna had measured the space she gained at her own property and decided the “big lady” would just fit in.
We assured her that Flax Mill was not closing (we haven’t done so for one day) and she landed with husband Peter and a sizeable trailer behind the car.
The loom was loaded and as they had moved up the lane a little sadness came over me – the old machine had gone on the second leg of its journey and would probably not come back here.
Conclusions which I think are important in those times:
- The loom’s journey took it from Ballymena to Derrylane and now to Cloughmills (where Lorna resides) which is just a few miles from its old home. Good to see it going “back to work” where it had operated for a long time!
- No money changed hands during the operation. The man who brought the loom didn’t want any, loved the thought of it finding a home. We didn’t have to pay for it so we didn’t have to charge Lorna, were delighted to see it going back to work. Marion like to sign letters “Love over Gold” – true if you give it a try, isn’t it?
- Finally: The “powers to be” told people during the time when the loom undertook its journey “…go to work only if essential…” or so. The loom will soon make fabric again (see pictures): Quiet, no carbon footprint, no long journeys for the products…Could you get it more essential – given the state of the planet??
Hermann Glaser-Baur
Flax blooms again in Belfast
Talented designer and Friend of the Mill, Deborah Toner, has nurtured flax in her back garden amidst the hustle and bustle of modern Belfast. Let’s hope this augurs the return of ‘the rippling sea of blue’ along the banks of The Lagan, once seen of old. Before exploring Deborah’s design expertise at her website , take a moment to enjoy the photos of the beautiful and delicate flax flowers she has shared with us.
Hemp with a natural tint
We’re excited to share some photos of a recent project, “Cannabis Tinctoria – We see colours”, from a past colleague and weaver here at the Flax Mill, Miriam Johnston. The photos record her investigation of transforming hemp yarn and fabric with a variety of natural dyes to produce stunning results! We’re delighted that she will be here with us to demonstrate her weaving skills at Open Day 2019.